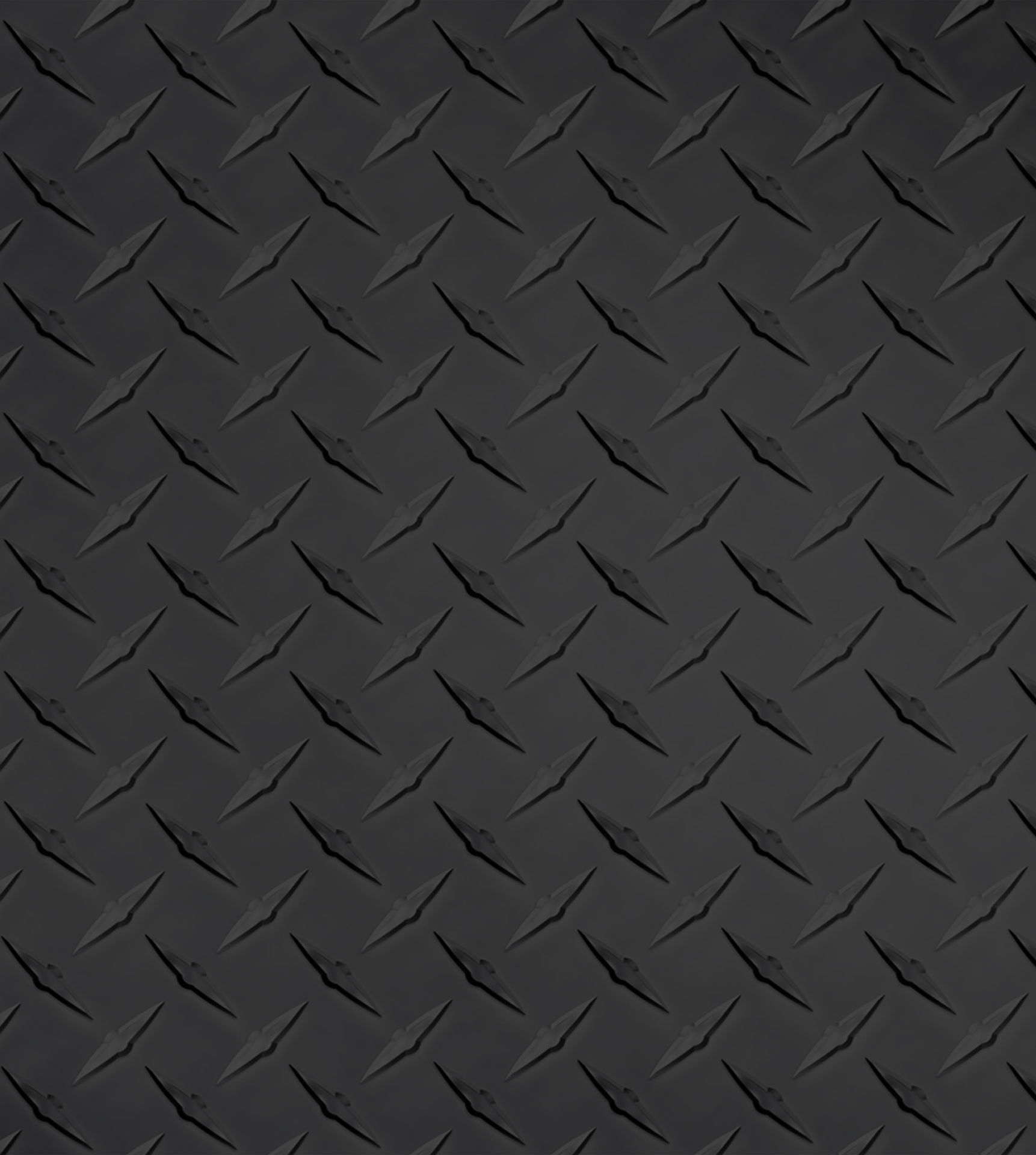
DEDICATION TO QUALITY
​
With multiple quality checks and a smooth operation flow, APR Plastic Fabricating has developed a solid fire truck tank construction process.
We start with an ultra strong, stress-relieved plastic material called Copolymer Polypropylene (CPP) which offers 10 times the impact-resistance of some other materials. Our CPP is made from high-quality resin and manufactured without impurities such as dirt and debris or other materials caused by regrind. With a longer life expectancy and virtually no maintenance, APR copolymer polypropylene fire tanks are guaranteed for the life of your service vehicle. APR designs meet the German Welding Society Standards (DVS) for construction and structural support. (Plastic welding originated in Germany, and in Europe is considered a professional trade.) APR’s superior fire tank construction involves taking the time to extrusion weld at every water-tight joint.
Our advanced baffling system acts as the structural support system for the tank, holding it together and minimizing splashing within. APR’s unique “finger-lock” design for longitudinal and transverse baffles add to the overall strength and durability of our tanks and meet or exceed NFPA requirements. All of our baffles are extrusion welded for superior strength, not bead or V-rod welded like some competitors do.
​
We believe in continual improvement in every area of our business, which is why APR maintains an ISO 9001:2015 Certified Quality Management System, implemented through all divisions and at all locations.
Step-By-Step: APR’s Fire Tank Construction Process
1) We begin with plans specified by the customer or can work with the customer to custom-fit a tank into an existing truck.
2) Once drawings are approved, our certified CNC technicians program the plans into our CNC router to cut individual pieces.
3) Pieces are bent and butt-welded per project requirements.
4) QUALITY CHECK: Pieces checked for accuracy and assembled into raw product.
5) Tanks are extrusion welded both on the inside and outside, completed by trained plastic welders.
6) Baffles are installed and extrusion welded, fittings and piping installed.
7) QUALITY CHECK: First water test check performed for leaks and capacity.
8) Lids installed and extrusion welded, fill towers installed.
9) QUALITY CHECK: Final water test completed and usable water checked (goal of 95% or higher).
10) QUALITY CHECK: Final quality control check before tank leaves the building to be delivered on time to the customer.
To learn more about APR’s fire tank construction process, contact us today.
QUALITY POLICY
"Continually improve the effectiveness of the quality management system in order to provide customers with quality products that are built to specifications and delivered on time."